Exclusive Interview | Dr. Shuai Li, Founder of FastForm: Exploring the Innovative Path of Metal 3D Printing
Recently, China's Chang'e-6 spacecraft successfully landed on the far side of the moon and returned with lunar soil, marking another great achievement in humanity's exploration of the universe. As the construction of the International Lunar Research Station gradually transitions from dream to reality, 3D printing technology, a core technology, has garnered significant attention. This includes the establishment of lunar soil 3D printing bases and the use of metal laser 3D printing in the first flight of the Long March 5 rocket.
Laser 3D printing, also known as metal additive manufacturing, has become an essential part of high-end manufacturing due to its flexibility in design, short development cycle, high printing precision, high material utilization, and excellent performance, especially suitable for complex structural components. In today's rapidly evolving technological landscape, 3D printing technology has expanded from small-scale research to large-scale application, deeply integrating into various aspects of life. Recently, we interviewed Dr. Shuai Li, founder and CEO of FastForm 3D Technology Co., Ltd. (referred to as FastForm), to discuss laser 3D printing technology and industry trends and development characteristics.
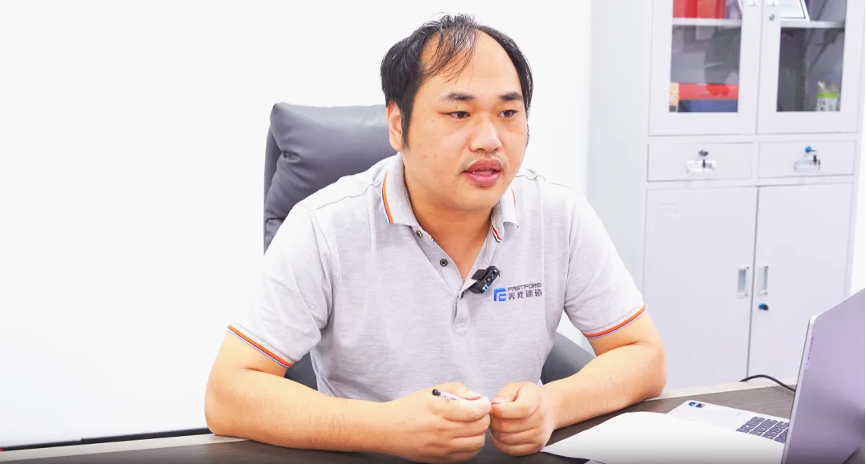
Dr. Shuai Li, Founder and CEO of FastForm 3D Technology Co., Ltd.
Embracing Integrated Innovation, Leading the Next Industrial Revolution
3D printing technology, originating in the 1980s, breaks the constraints of traditional subtractive and formative manufacturing by using digital printing to create complex three-dimensional structures, bringing disruptive innovation to the manufacturing industry.
Domestic and international universities and research institutions were the pioneers in exploring 3D printing technology. With continuous technological advancement, the aerospace industry has raised higher requirements for components, including ultra-high load-bearing capacities, extreme heat dissipation, and lightweight characteristics. Metal 3D printing technology can process refractory metals and alloys, and manufacture large-size, thin-walled, high-density, and lightweight components. More importantly, it can produce complex metal parts that are difficult or even impossible to process using traditional methods, such as thin-walled complex structures, non-standard curved surfaces, intricate flow channel structures, lattice structures, heat dissipation structures, and multifunctional integrated components.
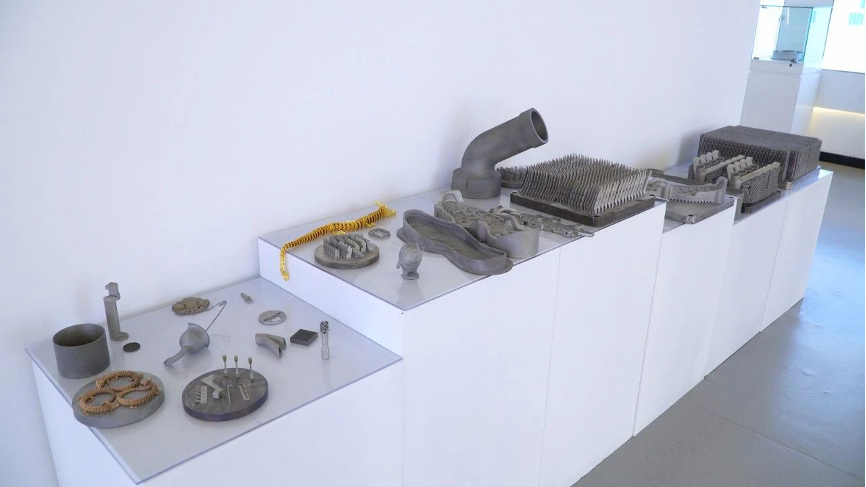
3D printed Metal samples by FastForm
Amid the industry boom, FastForm emerged in 2016. Leveraging the profound 3D printing expertise of Dr. Shuai Li and Dr. Zhichao Chen, both of whom are among the first batch of 3D printing Ph.D. graduates in China, FastForm quickly stood out. Both founders studied under Professor Yusheng Shi of the Additive Manufacturing Research Group at Huazhong University of Science and Technology, laying a solid foundation for the company's technological innovation. In 2021, FastForm relocated to Yancheng, Jiangsu, focusing on the research and development and manufacturing of Selective Laser Melting (SLM) equipment. The company adheres to a development philosophy that deeply integrates software and processes, continuously iterating software and optimizing processes, thereby not only localizing parts production but also significantly improving 3D printing efficiency.
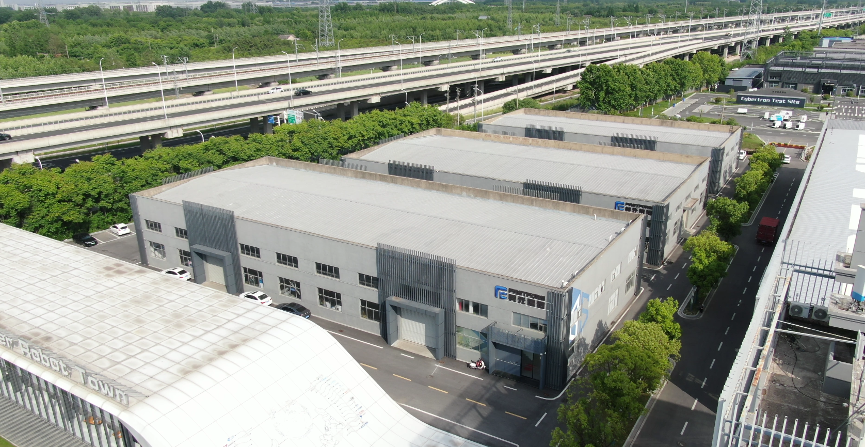
FastForm
Dr. Shuai Li stated that FastForm regards software algorithms as its core competitive edge, independently mastering key software algorithms, structural design, and control programs, and using software to define manufacturing. The company is committed to creating an open and cooperative platform for metal additive manufacturing. FastForm's independently developed slicing algorithms and control software have achieved numerous groundbreaking designs and innovations, meeting the customized needs of various industries for 3D printing equipment. On the hardware side, FastForm has launched a series of industrial-grade metal additive manufacturing devices, providing efficient and reliable solutions for aerospace, dental, and industrial mold sectors.
Over the years, FastForm has insisted on the integrated innovation of software, hardware, and processes. By optimizing software algorithms, improving processes, and designing complete machines, the company has achieved significant improvements in printing efficiency and substantial reductions in equipment costs. Additionally, the company has continuously optimized its after-sales service system to ensure a smooth experience for customers during use.
With its robust comprehensive strength, FastForm has made SLM metal 3D printing a tool for large-scale industrial production, achieving notable results in the 3C consumer electronics, footwear molds, and dental prosthetics sectors. To date, FastForm has shipped over a thousand units, ranking among the market leaders in terms of newly added metal SLM equipment market share in 2023. In the SLM dental equipment market, the company holds the top position. For instance, the M140C dental-specific machine can print over 1,000 dental prosthetics daily.
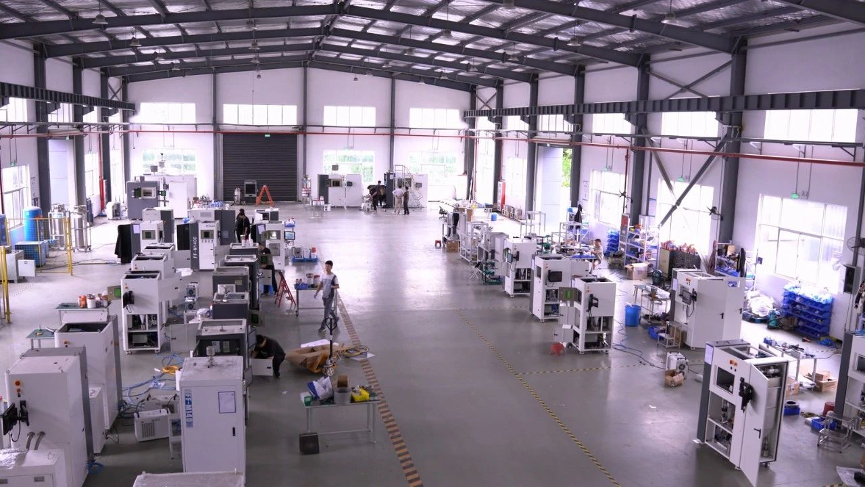
Panoramic view of the FastForm plant
Collaborating with BWT to Usher in a New Era of Domestic Substitution in 3D Printing
In the competitive 3D printing market, how does FastForm maintain its technological leadership and market competitiveness? Dr. Shuai Li emphasized that the company consistently drives innovation, continuously upgrading and making breakthroughs in software algorithms, equipment performance, and application expansion to ensure sustained technological leadership.
In terms of technological innovation, FastForm places great importance on close cooperation with upstream enterprises in the industry chain. Taking lasers as an example, FastForm has high requirements for the performance, service, and market reputation of lasers. During its cooperation with BWT, BWT's lasers have met the industry requirements for metal 3D printing in terms of spot size, beam quality, and stability. Additionally, BWT lasers have advantages in improving processing speed and miniaturization.
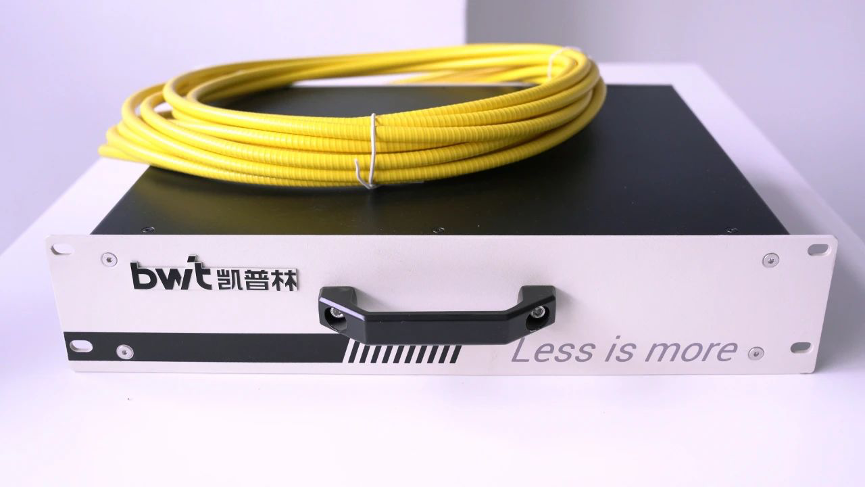
BWT's Lightning 500W Fiber Laser, with stable performance, is highly suitable for 3D printing equipment
Specifically, BWT's Lightning 500W Fiber Laser has become an essential assistant for FastForm in improving production efficiency and product quality due to its stable performance. For example, FastForm's M420 equipment can integrate up to eight Lightning 500W single-mode fiber lasers, significantly enhancing production efficiency while effectively saving equipment space.
Of course, domestic laser companies face challenges on the path to development in 3D printing. Among these challenges, timely service response and continuous technical upgrades and iterations are particularly important. Currently, BWT has a production base in Suqian, Jiangsu, ensuring timely after-sales service. They can quickly resolve various customer issues, essentially achieving a 1-minute response, 3-hour on-site service, and 6-hour fault resolution high-speed after-sales service channel.
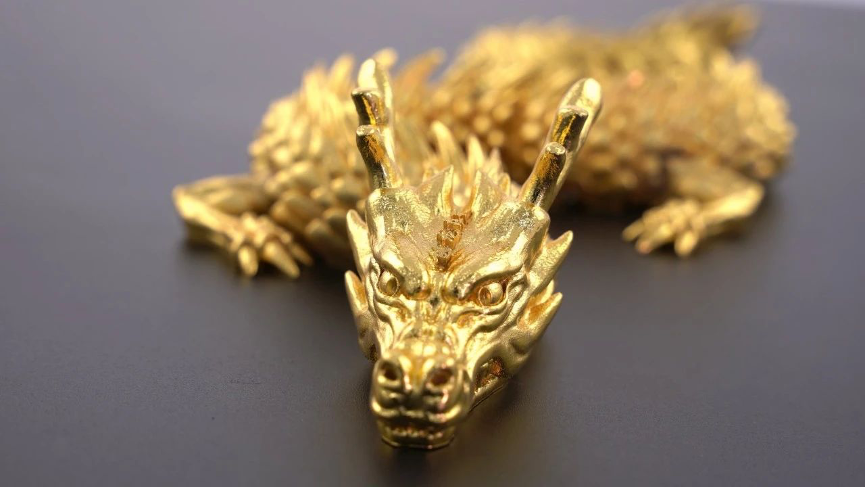
Artistic Loong printed by FastForm using BWT's Lightning 500W Fiber Laser
Globally, FastForm is accelerating its international expansion, with overseas sales accounting for nearly 30%, reaching Europe, America, Japan, South Korea, and Southeast Asia. As development accelerates, 3D printing companies need to achieve closer collaboration with industry chain partners in key areas such as lasers, software, and equipment, jointly promoting the global popularization and application of 3D printing technology.